ISTM
Overview
ISTM is a useful tool that supports component performance management or regulatory inspection activities with regards to valves, pumps, and heat exchangers in the nuclear power plants. Since it is a web-based system, data can be entered directly on the inspection site and analyzed in the office. Each component can be viewed on the respective drawing and previous data can be traced on site.
In-service test results can be judged in comparison to the previous data and reference values. ISTM supports safety effects evaluation of component test results by performing analyses using coupled fluid analysis program or reliability analysis program.
System Functions
- NPPs Drawing Presentation Service
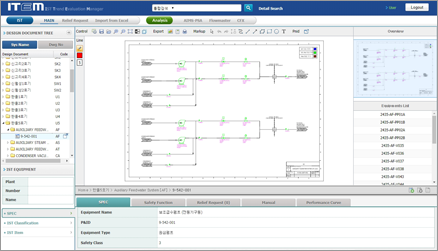
- Drawing verification through web-based CAD Browser
- Data verification of each component on drawing
- In-service test result management
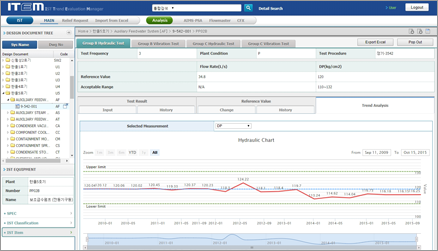
- Results management in-service tests of each component
- Interfaces for commercial analysis software
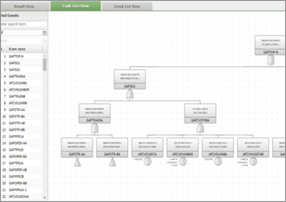
- Support Flowmaster program
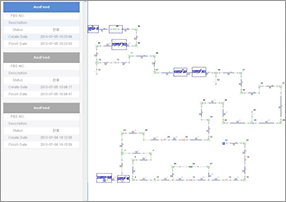
- Support CFX program
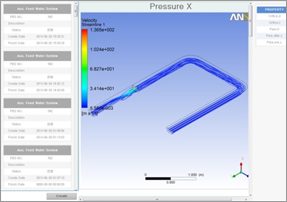
- Support AIMS-PSA program
- In-Service Test Management (ISTM) is a tool to systematically manage the performance, inspection history, and trend analysis data of the in-service test devices for nuclear power plants.
- Enhanced management efficiency and reliability through performance analysis, systematic history management, and quantitative performance management of in-service test devices.
- Enhanced user convenience and usability through web-based user-friendly GUI (Graphic User Interface).
Diagram of System
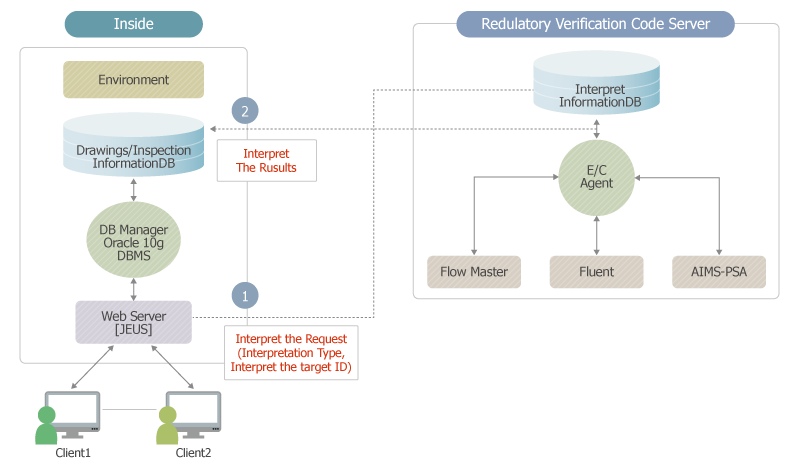
REPS
Overview
After Fukushima nuclear power plant accident, the emergency preparedness and responses to protect resident for the releases of radioactive materials from the nuclear power plant were a significant issue in nuclear industry.
To meet the demands, NSE is going to develop the computerized technical supporting systems.
Systecm Architecture
- REPS system is composed of ten evaluation modules. System functions are as follows:
- PAIS(Plant Accident Information System)
- CDAST(Core Damage and Source Term Assessment System)
- MeDAS(Meteorological Data Management System)
- REDAS(Radiological Emergency Dose Assessment System)
- RPA(Resident Protective Action)
- GIS(Geographic Information System)
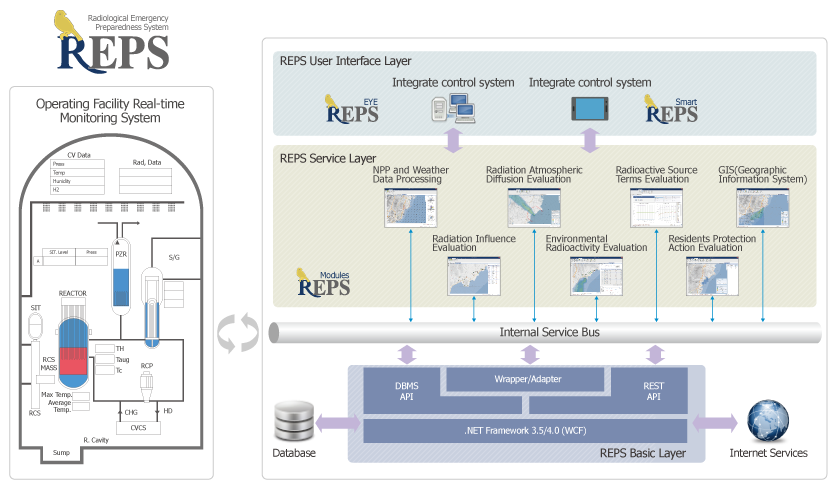
- REPS is a real-time information exchange platform to support emergency response activities (protective action of residents, guidance and etc.) during radiological emergencies in nuclear power plants.
- REPS supports resolutions to issues raised after the Fukushima nuclear accident in Japan, such as the evaluation of simultaneous accidents in multiple units at the same site, re-evaluation of emissions using environmental radiation monitoring data.
- REPS collects and evaluates weather data in real time.
PAIS and CDAST System
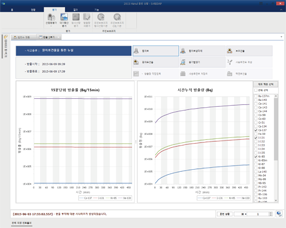
The PAIS system collects plant safety parameters regarding an accident or incident at all the nuclear power reactors in operation, and monitors the operational status on a accident situation.
MeDAS System
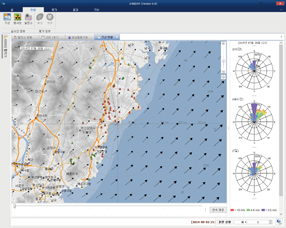
The MeDAS system collects regional weather forecast and local area measured meteorological data of the plant site.
REDAS System
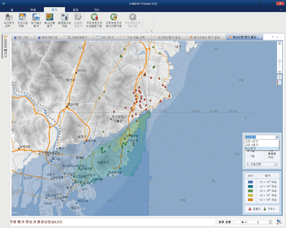
REDAS estimates doses to individual of the public from radioactive materials released into the environment to protect the public and the environment. The radiation doses are calculated using 3-D wind fields and source terms.
ERMAS System
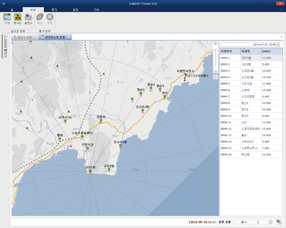
Radiation and radioactivity in environments are monitored during normal operation and accident situation. The ERMAS collects measured environmental radiation data from the stationary, temporary and mobile monitoring sites on real time basis and radioactivity data from sampling system.
RILAS System
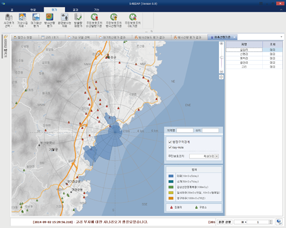
Protective actions during the Fukushima accident are taken by Japanese government to protect public based on recommendations proposed by the International Atomic Energy Agency(IAEA). The IAEA recommended protective measures should be implemented by the Operational Intervention Levels(OIL) derived from generic criterions.
RIXS System
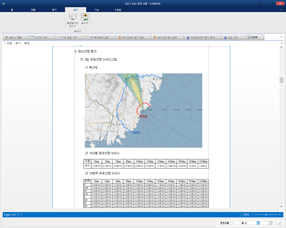
The RIXS is a web-based emergency response report and information exchange system that easily and quickly communicates and shares information among the emergency preparedness facilities in the case of an emergency exercise and/or real accident.
Major adventages
- Integrated with weather forecast data and NPP RMS system.
- Application of atmospheric dispersion model(AERMOD, CALPUFF)
- Evaluation of multi unit Accident
- Re-Evaluation of Source-Term
SIRIUS
Overview
SIRIUS is a title of a project which presents 'Weapon System SW Reliability Integrated Management System' for improving software reliability of combined weapon system. It is an on-going research in co-operation with Agency for Defense Development(ADD). To be internationally more adequate, SIRIUS meets the standards of IEEE 1633. ADD has all IP of SIRIUS.
Platform Architecture
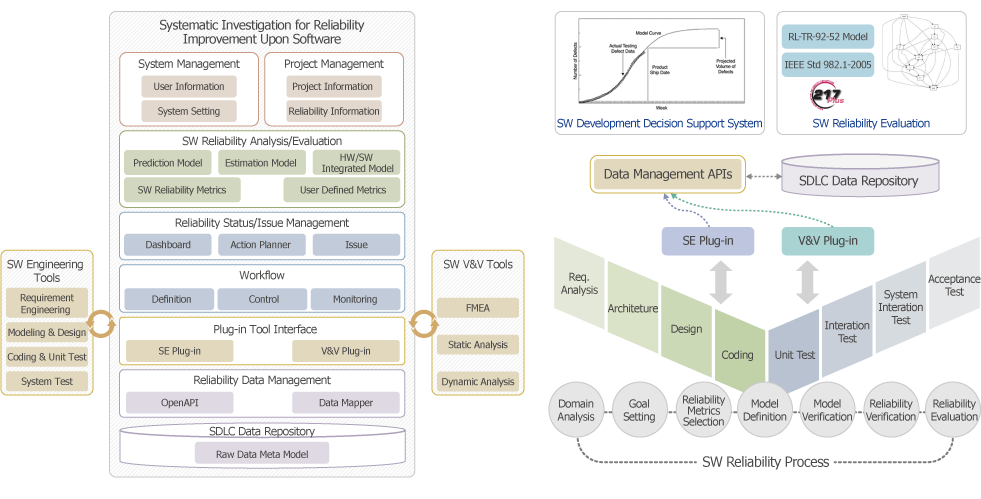
System Features
- System management
- Provides user information management and system administration.
- Workflow
- Define, control and monitor the workflow.
- Reliability Status/Issue (Dashboard)
- Function to manage issue generated during reliability process
- Function to assign and confirm tasks
- External interface
- Provides SW engineering tool plug-in and SW V&V tool plug-ins, SW engineering tools plug-in that can collect reliability related data through linkage with SW engineering tools and V&V tools.
- Project Management
- Provides functions to create, delete and manage project.
- Provides functions to identify reliability management items, to set progress metrics per development stage, to set defect type and severity, and to set target value per metric.
- Reliability Analysis/Evaluation
- Provides SW reliability metric analysis, SW reliability prediction modelling, and SW estimation modelling that calculate reliability based on data collected during SW development process.
- Function for identify the analysis results at specific times.
- Function for adding user defined metrics in addition to the 28 reliability metrics embedded in SIRIUS.
- Reliability Data Management
- Provides integrated function to manage all needed data to predict and estimate the SW reliability for the entire SW development stages.
- Provides application program interface (API) for interfacing with diverse commercial tools.
- Provides a scalable raw data meta model which can trace the inter-connections of all of the data of SW development processes and provides standard data architecture conversion (Data Mapper) function that can convert data based on this model.
SPLide
Overview
A software product line (SPL) is a set of software-intensive systems that share a common, managed set of features satisfying the specific needs of a particular market segment. SPLide supports the SPL framework as solution of SW integrated development environment. Currently research in co-operation with Agency for Defense Development is in progress. ADD has all IP of SPLide.
Platform Architecture

System Features
- SPL Process Management Tool
- SW platform development process and output management functions for weapon system
- Platform based SW development process and output management for weapon system
- Domain Analysis Tool
- Feature modeling capability for commonality/variability
- Function to extract the information of SW-based commonality/variability
- Function to create feature based platform requirement documents
- Plug-in function to support interoperability of requirement analysis tools
- Platform Architecture Design Tools
- Support for variable architecture design formats
- Function for the verification of consistency between feature model and architecture
- Plug-in function to support interoperability of architectural design tools
- Platform Implementation and Testing Tools
- Function for generating basic component source code
- Plug-in function to support interoperation of implementation and testing tools
- Platform based Weapon System SW development Tool
- Function for generating platform based SW output instance
- Function to verify the feature configuration
DECOM CMIS
Overview
DECOM CMIS is a Platform that supports Systematic Management of Physical and Radiochemical Configuration Changes for Decommissioning Requirements, Facilities, and Sites for Safe Decommissioning of Plant Buildings and Sites during Decommissioning NPP.
Platform Architecture
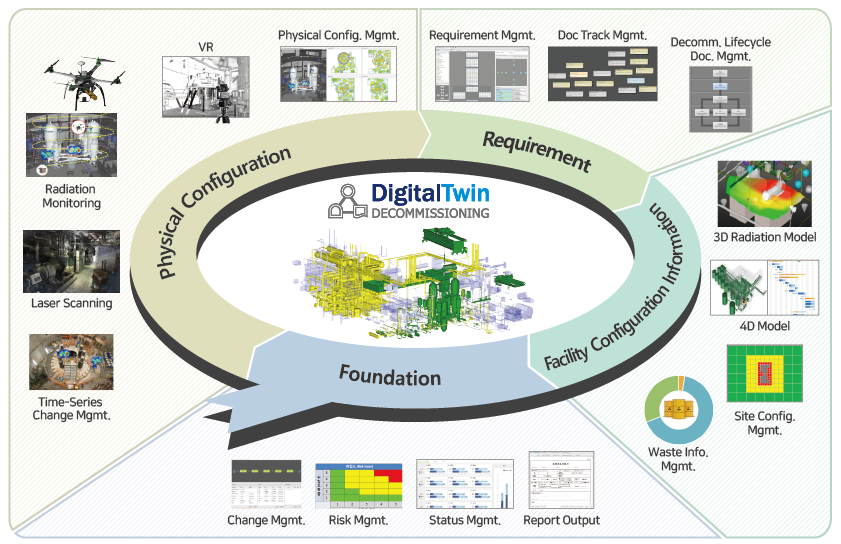
System Features
- Decommissioning requirement management, change management, life cycle document management
- Requirement management: Supports inquiry and linkage traceability confirmation for all requirements that must be considered in the decommissioning stage.
- Change management: Manages change management documents that occur during decommissioning.
- Life cycle document management: Systematically manages documents related to decommissioning strategies, decommissioning designs and methods, decontamination, and decommissioning activities.
- Site decontamination target achievement status and total waste information management
- Provides waste amount calculation function by level based on 3D model, material balance management, and contaminated soil management function.
- Digital Twin-based physical and radiological change management
- Provides function to manage integrated Digital Twin through linkage of D-BIM and radiation source, which is the basis of decommissioning shape management.
- 4th Industrial Revolution technology-based physical and radiochemical configuration change management
- Provides a system management function for physical changes through the function that controls drones and fixed PVR cameras.
- Manages physical configuration management and radiochemical changes of NPP.
- Provides information for decommissioning waste management and radiation protection technology support through 3D-based radiation models
- Identify potential risks during decommissioning work in advance, manage to avoid risks when they occur, and support to respond to the same situation in the future.
FAIR
Overview
Building a database for the Final Safety Analysis Report (FSAR) and applying an AI-based search system to enhance work efficiency in design changes, plant operation management, and prevent approval omissions.
System Functions
- Main Screen
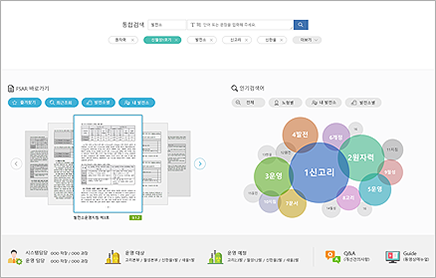
- FSAR Inquiry
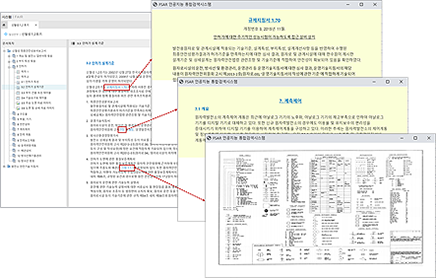
- AI-based integrated search
- Various shortcut functions (Favorites, Recent searches, By plant, My plant)
- View popular search terms by all, reactor type, my plant, each plant
- Inquiry of FSAR/TS by plant or chapter
- One-click search for related information through link in text
- Related information and traceability included in the selected section
- Inquiry of safety-related device information
- Linking of equipment and drawings related to the safety-related equipment list.
- Linking of documents related to the safety-related equipment list.
- AI based search
- Search results based on search terms (keywords).
- Search results based on similarity analysis with search terms.
- Search for inspection/audit data within the legacy system.
- Inquiry of revision history
- Inquiry of revision history by revision number and revision list.
- Comparison table before and after revision.
- Download FSAR, search results
- FSAR download by chapter.
- Download report on search results.
WTS
Overview
Radioactive waste tracking management system that integrates waste packaging-transportation-disposal management, data history management and monitoring, and disposal facility operation management.
Platform Architecture
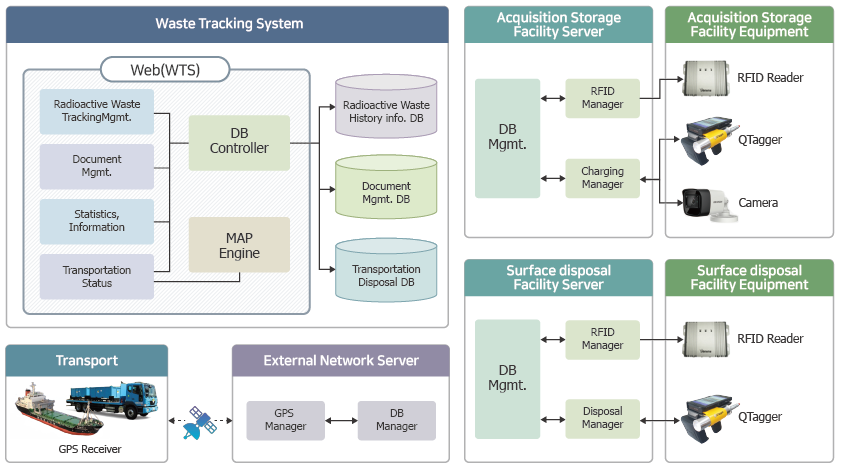
System Features
- Integrated Tracking and Management of Radioactive Waste History
- Manages all historical information of radioactive waste generated from occurrence to disposal and enables integrated inquiry of historical information based on the waste.
- Menu screens are composed of sequential function-based structures for high usability on-site.
- Enhancement of Convenience in Radioactive Waste History Management
- Automated management and validation of templates for radioactive waste information registration.
- Management of all historical documents based on radioactive waste.
- Management status and disposal radioactivity analysis function for analyzing radioactive waste status.
- Radioactive Waste Disposal Simulation Analysis
- Optimization of radioactive waste disposal in compliance with disposal capacity conditions and the total radioactivity limits for each disposal repository and radionuclide.
- Real-time Tracking of Radioactive Waste Transportation
- Real-time monitoring of radioactive waste transportation status equipped with a self-developed GIS engine.
- Evaluation of Compliance with Radioactive Waste Acceptance Requirements
- Automatic determination of compliance with acceptance criteria limits using data on waste generation characteristics when requesting acceptance.
- Automatic classification of radioactive waste packaging photos to support the evaluation of submitted acceptance materials.
E-DOSE
Overview
Dose evaluation system for routine radionuclide release from nuclear power plants. The system to supports the assessment of radiation exposure from gaseous and liquid radioactive effluents in KHNP ERP SAP network.
System Architecture

System Features
- Basic concepts of radiation dose assessment
- This is to evaluate the effects (radiation dose) on the human body and other people through various exposure routes after liquid and gaseous radioactive effluents discharged from a nuclear power plant are discharged outside the facility and spread through the atmosphere and ocean.
- Dose calculation by radiation path due to liquid effluents
- External radiation dose due to beach accumulation.
- External radiation dose due to swimming or water activities.
- Internal radiation dose due to consumption of seafood.
- E-DOSE system improvement effects
- Establishment of a network-based system to automatically link site weather and liquid/gas emissions.
- Establishment of a sharing based for dose conversion factors and half-life information that need to be shared by site.
- Clarification of data flow analysis between modules to secure data consistency.
- Dose calculation by radiation path due to gaseous effluents
- External radiation dose due to radioactive cloud.
- External radiation dose due to surface deposition.
- Internal radiation dose due to respiration.
- Internal radiation dose due to consumption of agricultural and livestock products.